Tube Benders & Tools
Mandrel-less and Mandrel Tube Benders for bending Tube and Pipe. Offered are both Electric and Hydraulic machines with NC and CNC Controls. All tube benders are customisable to suite customers specific requirements.
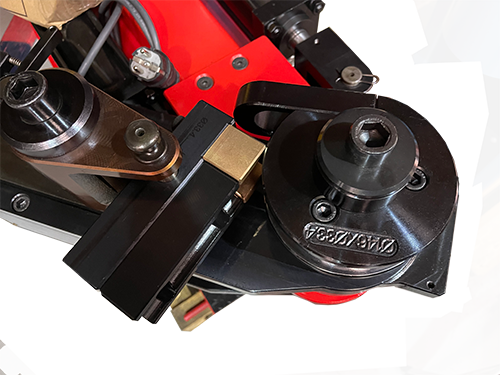

UK Expertise
1-3 Days Delivery
USA Sales
Nationwide Service
Ireland Sales
Fast Delivery to Ireland
Worldwide
Global ShippingWhat is Tube Bending?
Basics of Tube Bending Explained
Tube bending is a metal forming process for tubes used to form tubes into a permanent and desired form that can be used for a wide variety of applications and industries. Some common names for this process are Tube Bending, Rotary Draw Bending, Rotary Compression Bending, Mandrel Bending, Empty Bending, Crush Bending, Ram Bending, Profile Bending, Roll Bending, Ring Rolling, Section Bending, Push bending, Coil Bending, and many others. These terms are technically a specific forming process but are very often used interchangeably, but this article addresses Rotary Draw Bending.
Tube Bending Machines are either manually powered or powered by a drive mechanism such as hydraulics, electric motors, or servos. The bending process itself for this discussion falls into two categories the first being Empty bending. Empty Bending relies on the tube’s physical structure to support itself during the bending process. The second process is Mandrel Bending which implements alternative tooling components to support the tube during the bending process. The main component of this toolset is the Mandrel. The Mandrel internally supports the structure of the tube typically at the tangent point of the bend.
The majority of tube bending is with round tubes, but Square and Rectangle Tubes can also be bent along with various Profiles such as Equal Angles, T-Sections, Extrusions, and U-Sections. The tubes are profiles bent in rotary bending applications are typically made from Mild Steel, Stainless Steel, and Aluminium, but there are also tubes used in tube bending applications that are made from more exotic metals such as Titanium, Inconel, Incoloy, Hastelloy, and Chromoly to name a few. When purchasing tubes or pipes for bending applications, it is essential to consult your stockist to ensure that the grade of material you are purchasing is a bendable grade of material.
There are various terms and measurements used to define a bend with tube bending, and the most common term is the Bend Radius. This term refers to either the Inside Radius (IR), Outside Radius (OR), or the most commonly used term, Centre Line Radius (CLR). The easiest way to determine the CLR of a bend is when a tube is bent in a U-Shape, you can use a ruler to measure the distance from the centre of the left-hand leg to the right-hand leg then divide that measurement by 2. That will give you the CLR. Other methods to determine the CLR of a bend, such as tracing and digital measuring systems, are used.
To accurately discuss a tube bending application, the Tube Dimensions and Parameters must be accurately defined. A wide variety of terms are thrown around when discussing Rotary Bending Applications. Still, the most common and important terms are Outside diameter (D), Wall thickness (W), the Type of Material, as discussed above, and the parameters referring to the bend itself being the CLR. When talking about tube and pipe bending applications, CLR is often referred to as Times “D” or “xD”. For example, if you are bending a 25 mm outside diameter tube on a 100 mm CLR, then it is a 4xD Bend. From experience, the most common bend is typically a 3xD bend. It often ends up being the threshold to where Empty Bending can be carried out, but this can vary contingent on various factors. Beyond that, the same tube bent on a 2.5xD CLR would require a Mandrel Bender or the bend would fail. If the threshold is reached, Necking, Wrinkling, Ovalisation, and Kinking can occur. Note that in some applications, Necking, Wrinkling, and Ovalisation are acceptable.
A quick way to summaries and evaluate the threshold for bend failure is to us what is called the Wall Factor (WF), which is simply the ratio of the Outside Diameter (D) of the tube to the Wall Thickness of the tube (W), or D/W. An example using a 50 mm diameter tube with a 2.5 mm wall: Divide the D = 50 by W =2 and you get a WF of 25. The same tube with W=10 produces a WF=5. Yet again, the same tube with W=1 makes a WF=50. The larger the WF is, the larger the CLR that is required. The WF is according amplified or reduced contingent on the tensile strength of the material the tube is made from.
As mentioned above, for most applications, 3xD is the threshold for crossing over from Empty Bending to Mandrel bending. I have seen where alternatives to mandrel bending are used to achieve a tighter CLR, such as bending springs, inserting a concentric tube inside the bend tube, or packing the tube with sand. I have even seen where the end of a tube is welded shut with a cap and then filled with water, and then put into the freezer. The water inside the tube freezes, essentially making the ice a bending mandrel. These processes can work, but these are more of a hack than a bonafide production process. These processes are also time-consuming, and the results are at the best varied. For very accurate, efficient, and repeatable bends, a mandrel bender must be used.
Mandrel Bending employs all the same basic concepts as empty Bending, but a Mandrel Rotary Draw Tube Bender is a more complex machine with more machine and tooling components. But once the overall operation and concepts of a Mandrel Bender are mastered, the bending functions that can be complete are limitless, and the bend quality is unbeatable. The same parameters are used and discussed, and from experience, the typical CLR in Mandrel bending is 2xD but other CLRs are very common, such as 1.5xD, 2.5xD, or even 1xD or less.
The Components of a Mandrel Bender Tooling Set includes the Mandrel, a Bend Die, a Clamp Die, a Wiper Die, and a Follower Die. There are variations of each of these components that can address a wide variety of applications. The tool set components are manufactured from a variety of metals suitable for tools and ideal for the bending application being addressed. There are two basic types of mandrels: the first being a Straight Mandrel, or in the field it can be referred to as a Bullet Mandrel due to its overall shape looking like a bullet. The second type of Mandrel is an Articulated Mandrel, which is a Straight Mandrel with the end cut off and with Mandrel Balls attached to the body with linking chains. An Articulated Mandrel looks lie a rattlesnake tail and can have multiple balls that allow the Mandrel to extend well beyond the bend’s tangent point. Mandrels are made in a wide variety of shapes and forms and from a wide variety of materials. Still, the Straight and Articulated Mandrel are the most common mandrels employed in Industry.
Mandrel bending is used in a wide variety of applications in a vast quantity of industries. Some typical applications and Industries are HVAC, Refrigeration, Petrochemical, Playground Equipment, Fitness Equipment, Transportation, Rail, Agricultural Equipment, Pneumatics, Ductwork, Tanks, Vessels, Street Furniture, Signage, Sculpture, Construction, Architecture, Furniture, Aerospace, Automotive, Heavy Trucks, and Shipbuilding.
The Aerospace Industry is known for its tight tolerances and exotic materials. Aerospace Manufacturers implement Mandrel Benders to produce fuel lines, hydraulic lines, exhaust systems, engine ductwork, and tubing and seat frames.
The Automotive Industry as well is known for its tight tolerances and high-volume production requirements. The Auto Industry uses mandrel benders for fuel lines, exhausts, cooling systems, brake lines, and fuel lines.
The Heavy Truck Industry requires precise and small bends and often completed on difficult-to-bend and high-strength materials such as 304-grade and 409-grade stainless steel for fuel lines, engine cooling tubes, structural items, safety railings, and boarding ladders.
The Shipbuilding Industry is a comprehensive industry that manufactures ships from small commercial vessels to large freighters. The infrastructure in these ships includes waters pipes, fuel lines, HVAC, Electrical Conduits, Wastewater Lines, Fresh Water Systems, Hydraulic Systems, Exhaust Systems, and a wide variety of bent tube and pipe.
These industries require the utmost accuracy and repeatability to meet their quality standards on a minute-by-minute and day-by-day basis. Their requirements change continuously, and the requirements are complex, so the implemented manufacturing systems need to be top-quality and must be able to evolve with their products over time. The Workshop Press Company offers Flecte Mandrel Tube Benders explicitly designed to meet the requirements set forth by these industries. The Flecte range of Automatic Mandrel Tube Benders implements brushless motors to control the bending axes. The wide variety of available features and accessories ensures an automated bending machine that is very versatile and can address the most diverse applications and components. FLECTE is an Italian company that manufactures a line of Electric Tube Benders with a modern design and an all-electric design suited for the Automotive, HVAC, and Aerospace industries bending requirements which require the most stringent requirements of accuracy, reliability, flexibility, and speed.